The first cuttings of hay are done at Sand Creek Dairy in Hastings, Mich. Soon, Ethan Haywood and his family will shift their attention to corn silage, the energy powerhouse that helps fuel milk production on the 1,200-head dairy.
Like clockwork, the farm’s six full-time shop employees will switch over the Claas 970 10-row chopper to a corn silage setup.
“They will work like a NASCAR pit crew swapping things over so we can start taking moisture samples out in the fields,” Haywood says. “They will get the kernel processor in and set. They will typically flip the shear bar. They will have inspected the head knives, and typically, we’ll put a new set of knives within the chopper itself. And then with this chopper, we also have to insert a spout extension, and we’re pretty much ready to roll.”
Not every farm has the luxury of six full-time people working in the shop. But good crop quality should be the goal of every dairy, regardless of size, says Shaun Fritchey, John Deere’s self-propelled forage harvester specialist.
“What’s being chopped today will feed the cows the next 365 days,” he says.
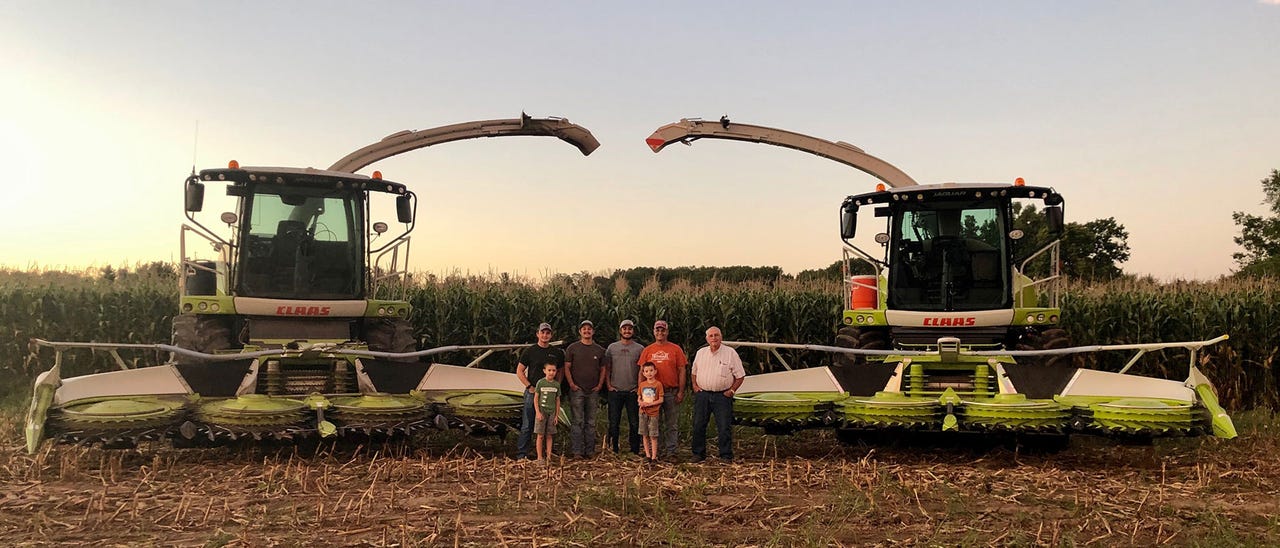
SAND CREEK CREW: The Haywood family — (back, from left) Devin, Ethan, Austin, Luke, Larry, and (front) Brenden and Colton — focuses on growing and harvesting high-quality forage for their herd at Sand Creek Dairy. Their forages have been recognized in the World Forage Analysis Superbowl and have contributed to a Jersey herd average ranked among the top 10 in the nation each of the past five years for at least one measure of production. (Photo courtesy of Michele Ackerman)
Preharvest preparation is key to transitioning a forage harvester to a corn silage setup. Fritchey has a few tips.
“Change the cutter-head knives from grass knives to corn knives. Ensure those knives are new, [and] torqued correctly to the operator manual,” he says. “The next biggest thing is the kernel processor. It’s always a good idea to have those … rebuilt after the season in terms of having new rolls ready to start the season; that the gap has been verified and it’s correct; that the rolls are in balance and haven’t shifted side to side because of wear; and then also inspect the bearings to ensures the KPs [kernel processors] have not drawn any moisture in the offseason.”
Calibrating the various mass flow sensors on the machine is also key, Fritchey says. It typically involves harvesting specific loads, measuring the actual weight of those loads, and then comparing that weight to the sensor's readings.
Here’s an in-field example:
“The chopper will pull into the field, fill a truck, and the machine will say it weighs a certain amount of pounds,” Fritchey says. “The truck then goes to the scale. He radios to the operator in the forage harvester, and changes the tonnage and calibrates, and the chopper and scale will read the same amount. Now, it’s not perfect, so those numbers will never be exact, but they’ll be close.”
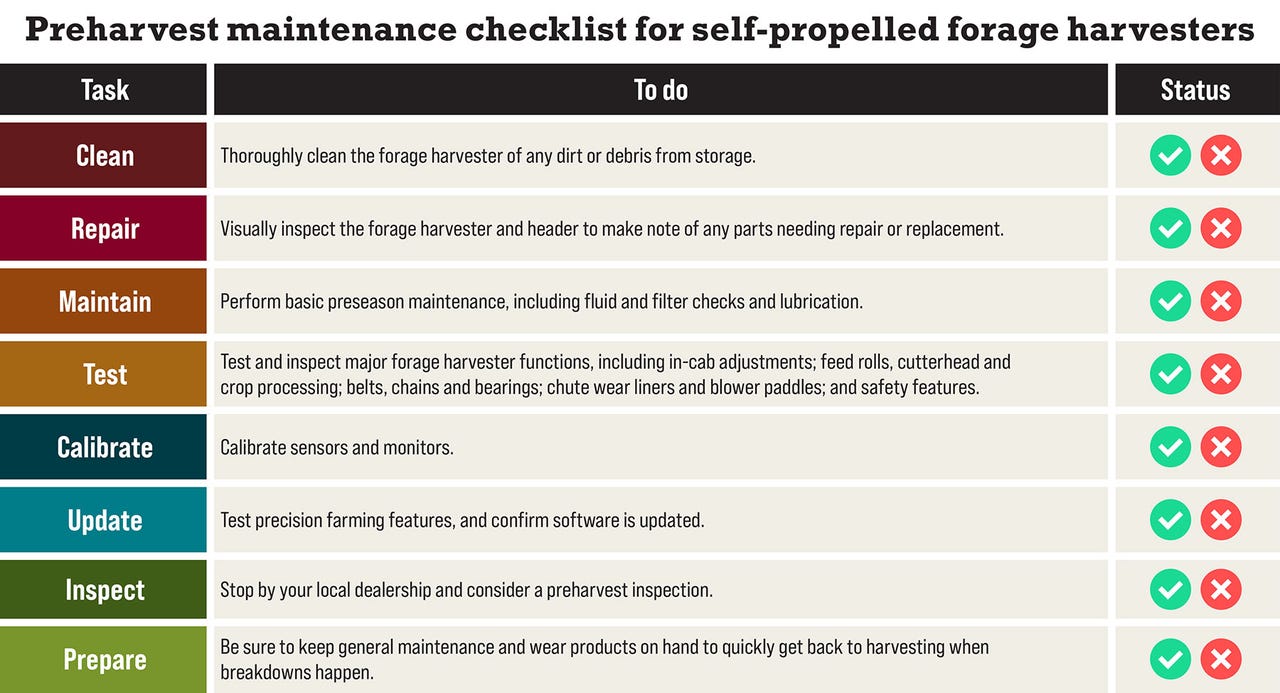
Keep things clean
Once harvest is over, Haywood says his crew power-washes the chopper, blows it out with air and regreases various parts before it gets stored for winter.
Next spring, the process starts all over. “We inspect a lot,” he says. “We look for critters, animals and damage they may have done. Once that’s done, we run it through the shop, look at seals and bearings, regrease, and get ready for first-cutting hay.”
This might sound basic, but staying on the regular maintenance schedule is something many farmers often overlook, Fritchey says.
“And just the cleaning,” he says. “These guys are spending a tremendous amount of time in these machines, day in and day out. Some of these guys are starting toward the middle or latter part of April and won’t be done until November. It’s always a good idea to do the cleanings and inspection at the end of the run when you’re done with the season. Open those shields up, get the compressed air in there, wash it, whatever.
“One thing customers are becoming more accustomed to doing is cleaning the kernel processor,” he adds. “Pulling the rolls out of the KPs, blowing it out, leaving it disassembled and open up so you can clean it with air. Just cleaning the rolls to get the crop juices out of it and allowing that machine to air dry.”