Dusty Hininger, sales training manager at Firestone Tires, says he often finds himself on a soapbox.
“I just preach and preach and preach,” he says. “I would say at least half of farmers don’t know what air pressure to run, because that is the No. 1 question I get from farmers.”
Especially during an economic downturn when every dollar counts, guesses aren’t sufficient. That’s because the top issue affecting tire efficiency — which equals dollars — is air pressure.
“The bigger the footprint in the field, the longer the tire will last. They wear longer, so you don’t have to replace them as quickly,” he says.
Hininger estimates that driving an ag machine with optimal tire air pressure, which creates a bigger tread footprint, can extend a tire’s lifespan by as much as 10% to 20% due to even wear.
There are other benefits to closely monitoring tires, like decreased slippage in the field, which makes machines more efficient.
Tractors rolling on properly inflated tires make faster passes and take fewer fuel stops, saving time and input expenses. Hininger says that just a difference of 10 pounds per square inch can save up 5% in fuel costs. The soil is healthier, too.
“Compaction is a big, big, big dollar figure,” Hininger says. Crops tend to be detrimentally impacted when tire pressure crests 15 psi. “It’s a 4% to 6% loss if you’re above 15 psi.”
Damage is compounded when more than one machine has overinflated tires. It all adds up. While many variables exist, Hininger calculates that correcting air pressure can save around $35,000 for a 1,000-acre corn operation yielding 200 bushels per acre, the nationwide average.
“Say I’m a liar,” he says. “Half of that is $17,500. Isn’t it worth it to weigh your equipment and start checking air pressure?”
Daily maintenance
Hininger suggests checking air pressure first thing each morning. Tires build up heat throughout the day, so later readings might be inaccurate. It’s a 15-minute chore that pays dividends, given that a tire pressure gauge costs around $20, and the savings could be enormous.
“Farmers check the oil on their tractors. Why? Because that engine costs many thousands. Well, tires also cost a lot, too,” he says.
But while the benefits to proper tire inflation are clear, there is a caveat: Older tires that have never been inflated or deflated regularly should not be adjusted.
“I wouldn’t take tires that are 10 years old and start adjusting the air pressure on it. As that tire rubber gets older, it gets harder,” he says. “It may cause it to crack. The rubber is already hard, and it never [flexed] during its life cycle.
If that’s the case, Hininger says to just run them as is until they wear out.
“When you buy new tires, please adjust them, because it will save you,” he says.
Finding right weight
The first step to correcting air pressure is to weigh your machine — either yourself or by contacting a dealer — and the implements it pulls. Each piece of equipment is different. Many variables exist besides weight such as proper weight distribution, field conditions and PTO horsepower. Counterweights might need to be added for balance.
Some tires are better than others, and tools on the market can optimize air pressure changes. Tires labeled VF, for very flexible, can use 40% more load or they can lower their pounds per square inch, reducing soil compaction.
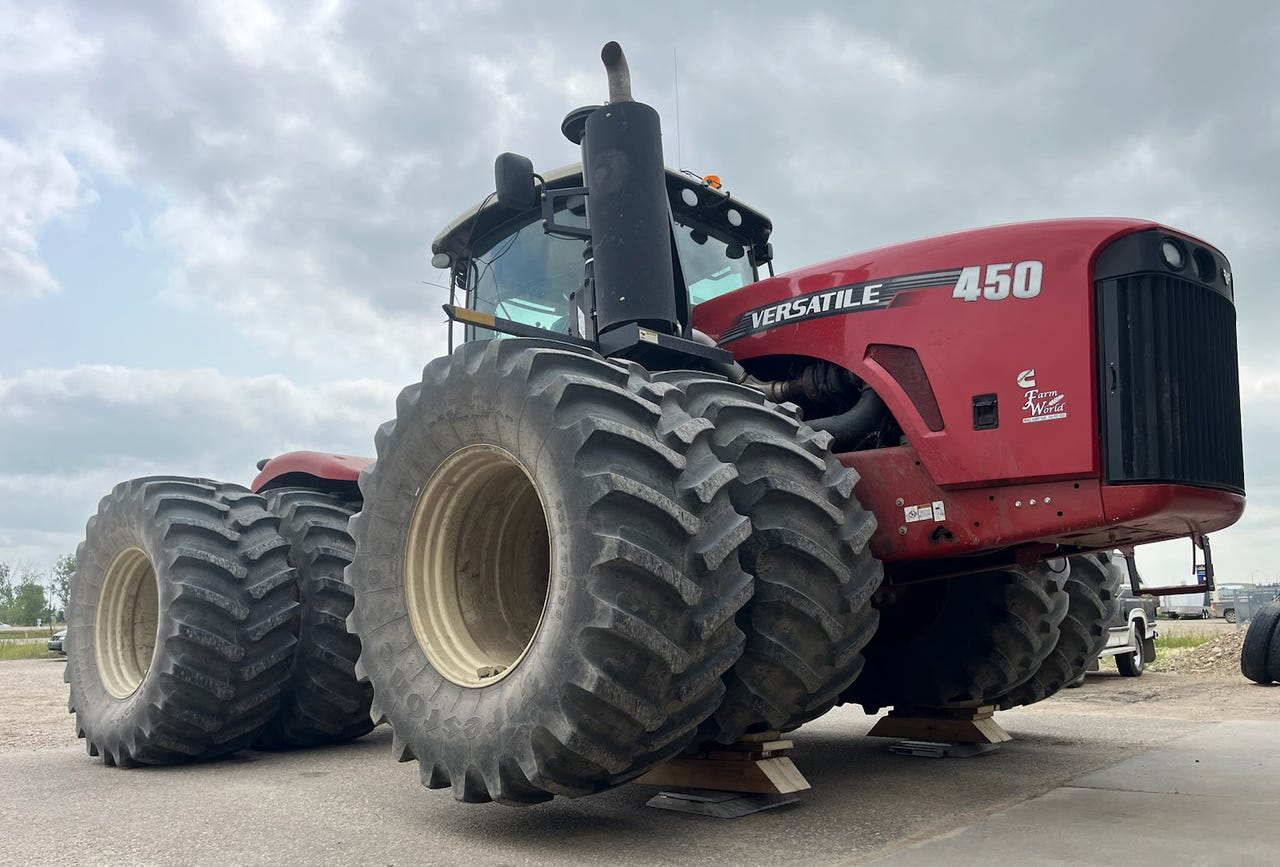
INFLATION MATTERS: Tractors rolling on properly inflated tires make faster passes and take fewer fuel stops, saving time and input expenses.
Tire inflation systems, which cost about $30,000, pay for themselves through fuel savings by adjusting air pressure on the fly — less than 15 psi for fieldwork and about double on roadways.
“When we get on the road, there’s a little thing called rolling resistance,” Hininger says. If setting tire pressure the same as a standard tire carrying a load, “you’ll have less resistance, and that tire will save fuel going down the road. So, you’re saving fuel both ways.”
Hininger travels across North America and Australia talking to farmers about tire health. Sometimes, he says even dealership representatives are surprised to see just how far off their inflation calculations are. He recently returned from a trip to Canada and recalled a conversation he had with one farmer.
“I said, ‘OK, what air pressure should that tractor be at?’” he says. The farmer looked at his machine and guesstimated its correct pressure based on the number of bars on the ground.
“All I said was this: ‘It has nothing to do with that. You have got to weigh the machine. You can’t look at a tire and say, ‘There’s 10 psi less in the tire.’ I mean it. You just can’t tell. And with VF tires, you can go with less air pressure. It’s just amazing what you can get by with. But you have got to weigh it before you can do that.”
How to calculate pressure
For more information on tire pressure, reach out to your local tire representative. Follow these steps to calculate optimal air pressure:
1. Identify the tractor’s horsepower.
2. Calculate the weight needed for proper setup based on its type:
- For two-wheel drive, multiply 145 pounds by the PTO horsepower.
- For mechanical front-wheel drive (MFWD), multiply 130 pounds by PTO horsepower.
- For four-wheel drive, multiply 110 pounds by the engine horsepower.
3. Calculate the recommended front- and rear-axle weight splits based on the tractor type:
- 2wd — front at 25% and rear at 75%
- MFWD drawbar — front at 35% and rear at 65%
- MFWD three-point hitch — front at 40% and rear at 60%
- 4wd — front at 51% to 55% and rear at 45% to 49%
4. Weigh the tractor to determine its actual weight.
5. Add or remove weight to the front and back for optimal tractor setup.
6. Set inflation pressure using an online tire inflation calculator such as the one at firestone.com.